Perth Insulation keeps your home warm in the winter and cool in the summer. It decreases the amount of energy required to keep you comfortable and lowers your energy bills.
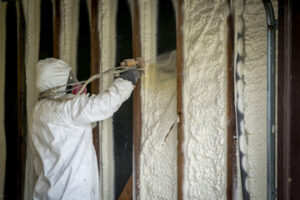
Insulation reduces heat flow through conduction, radiation, and convection. It is commonly installed in walls, attics, and floors. It comes in batts and rolls, blown in with special equipment, or as spray foam.
Fiberglass insulation is the most common type found in homes. It’s made from recycled glass and sand particles that are heated and spun into finely-tuned fibers. Binding agents and additives are incorporated into the mixture before it’s formed into rolls or batts. The products are then cured in ovens before they’re packaged for use.
While fiberglass has its benefits, it’s important to know the limitations of this insulation material. Its biggest drawback is that it doesn’t provide a complete barrier against airflow through walls and ceilings. This enables the movement of hot and cold air, which can result in higher energy bills and uncomfortable rooms.
In addition, fiberglass can absorb moisture and lose its insulation effectiveness. This type of moisture is particularly dangerous in areas like basements, where it can lead to mold and mildew. The moisture can also damage the framing of a home’s structure.
Another drawback to fiberglass is that its fine fibers can lodge in the pores of a person’s skin, leading to itching and rashes. Fiberglass is also not completely fireproof, and when it burns, it releases a harmful gas. While it smolders before actually burning, the gases released can still be harmful to a person’s heart and lungs.
The good news about fiberglass is that it’s an inexpensive and easily accessible option for homeowners looking to add insulation to their homes. It’s available in rolls and batt form in many different sizes to fit standard stud and joist spacing. This makes it a convenient choice for DIY projects, and it’s usually available in your local hardware store.
It’s also an environmentally friendly option, as it is made from recycled glass and can be recycled again after it’s used in a new home. In the past, some manufacturers treated their fiberglass with formaldehyde, but most companies now produce it using an energy-efficient process that produces fewer carbon emissions.
It’s also worth noting that fiberglass has acoustic properties, reducing the amount of noise that passes through a wall or ceiling. However, the exact level of sound reduction depends on its thickness and density.
Mineral Wool
Mineral wool insulation is a green product that has many benefits over fiberglass batts. For one, it resists thermal drift better than fiberglass and has a higher R-value per inch of thickness. It also doesn’t rely on injected gases to maintain its insulating performance, and it doesn’t leak moisture or provide food for microorganisms.
Another advantage of mineral wool is that it has superior sound attenuation. This makes it a good choice for commercial and industrial buildings that need to reduce noise levels, such as natural gas compressor buildings and stations. The material also offers fire resistance and has a high melting point.
The material is produced from a combination of primary raw materials, such as basalt, diabase and dolomite (stone wool) or sand, limestone and soda ash (glass wool), and secondary, recycled raw materials, including cullet, iron ore slag and steel mill shavings. The combined materials are sent from feeders into a melting furnace. They are then shaped and cut before being bundled into sections, commonly referred to as “batts.”
While the material has numerous advantages, it does have some drawbacks. Historically, the insulation contained chemical binders that off-gassed volatile organic compounds, which negatively impact homeowners’ indoor air quality. However, this issue has been largely resolved due to a move toward low VOC binders.
The other drawback is that the insulation has a high embodied energy footprint, as it requires a special furnace for manufacturing and high temperatures to be maintained in the melting process. This high energy consumption has led some people to question its sustainability. However, manufacturers are working to offset this by using less energy and reducing waste, and many of the materials used in the insulation are recyclable.
Like fiberglass, mineral wool is available in a variety of thicknesses and R-values. It is commonly available in both rolls and batts, and is easy to cut and install to ensure it fits the space correctly. However, it is heavier than fiberglass and may not offer as much acoustic control. It also needs 3.5 inches of thickness to reach R-15, while polyiso requires 2.5 inches to achieve the same R-value.
Cellulose
Cellulose insulation is made from recycled paper products, including old newspapers, cardboard, and office papers. It’s a green alternative to fiberglass, saving energy and reducing waste. The material has a high R-value that prevents conductive heat transfer.
It also helps halt convective flow of heat, keeping cold air from seeping into walls in the winter and hot air from infiltrating attics in the summer. The material also has a high sound transmission rating, meaning it reduces noise.
Blown-in cellulose is safe for you to touch and can be installed in the walls and attics of your home. It’s composed of 85% recycled content, with most of that coming from post-consumer recycled newspaper. The remainder is treated with boric acid, which works to repel pests and mold. In addition, the material has an acrylic binder that slows down its deterioration over time.
In its dry and loose-fill form, cellulose is used to retrofit old homes and fill new wall construction. It’s blown into holes drilled in the wall and held in place by temporary retainers or netting that’s removed once it reaches an appropriate density. It’s also available in a spray-applied form that doesn’t require the use of these retainers.
Both forms of cellulose are treated with fire retardants to meet federal, state/province, and local building codes. While there’s been some static over whether cellulose is safe, independent testing has concluded it’s just as fire-safe as fiberglass insulation. It’s important to note, however, that it does absorb water, which could cause a fire hazard if it’s allowed to accumulate inside walls or attics.
Loose-fill cellulose is easy to install because it can conform around obstructions in walls and attics, such as wiring and ducts. It’s also a good choice for attics with a low roof slope since it will stay in place better than other types of insulation. It’s best to hire a professional contractor to perform the installation, since it requires proper equipment and knowledge of building code requirements. Those who work with the insulation should wear personal protective equipment like safety glasses, gloves, and a mask to avoid breathing in the dust.
Spray Foam
Spray foam insulation is sprayed onto walls and roofs of homes and commercial structures. It is sprayed on site and expands, filling in all the nooks and crannies, to create an airtight seal that helps improve energy efficiency. It is more expensive than fiberglass insulation, but it is also more effective.
Unlike traditional fiberglass or cellulose, foam insulation also acts as an air barrier in addition to being a great insulation material. Some studies show that up to 40% of a building’s energy is lost due to air infiltration. The air leaks are caused by gaps, nooks and crannies, and uninsulated spaces that let air escape and increase monthly utility bills. Spray foam insulation closes these areas by acting as both an insulation and a sealant, making it more efficient than traditional fiberglass and cellulose.
A professional insulation contractor can help you choose the type of spray foam that is best for your home. There are open-cell and closed-cell spray foams, with the closed-cell variety being more durable and acoustically superior. Some brands are also greener than others. For example, the closed-cell spray polyurethane foam HEATLOK SOY is made from recycled plastic waste to help conserve nonrenewable resources.
The process of installing spray foam insulation starts with removing any existing insulation in the area being insulated. Depending on the area of your home or commercial structure, this may include ceilings, walls, and floors.
After removing existing insulation, the crew will apply a primer to the surface to ensure the spray insulation adheres. Then, the installers will spray on the open or closed-cell foam to cover all surfaces. It will expand up to 100 times its original size, sealing the nooks and crannies that can let unwanted air escape.